Introduction
In our first post, we presented the framework for Project Earth.
We will begin our journey exploring the greenhouse gas (GHG) emissions from the most significant contributor, making things.
How Much Greenhouse Gas is Emitted by the Things We Do?
Although manufacturing is the most important contributor to emissions, the media generally focuses on other activities. And understandably so, since most people aren’t interacting as much with this segment. We don’t think about the steel pipes in our homes or the concrete paved on the roads we walk on, but this segment is everywhere. In contrast, it’s hard to go a week without having a conversation about plant-based meats (growing things) or electric vehicles (getting around).
Let’s dive into our first subject, concrete.
Sources of Emissions
Concrete is everywhere. Second to water, concrete is the most widely used substance globally. Without concrete, we wouldn’t have any of the infrastructures you see around you – bridges, roads, airports, or homes. In 2020, we produced 4.2 billion tons of concrete, representing a volume of 14.0 billion m3. By 2050, we are expected to produce 5.5 billion tons of concrete.
Why is concrete used so much? Because it’s strong and easy to make. The raw materials used to make concrete are widely accessible, and concrete is sturdy and resistant to fire and water.
Unfortunately, concrete production emits a significant amount of GHGs. It is responsible for 6% of the world’s GHG emissions and about 8% of global carbon dioxide (CO2) emissions - that’s close to ~3 billion tonnes of CO2 annually. It would be the third-largest CO2 emitter behind China and the United States if it were a country.
The culprit behind concrete’s significant GHG emissions is the cement used in its production. Cement serves as the glue (the technical term being binder) that creates concrete when mixed with gravel, sand, and water. We use various materials to make cement, but the critical ingredient is limestone. During the cement production process, limestone is heated to an extremely high temperature of 1450°C in a large cylindrical container called a kiln. This activates a chemical reaction (calcination) which breaks down limestone into calcium oxide (what we need in cement) and CO2 (the unfortunate by-product). The calcination process requires a lot of heat. Most of the time, we generate the heat required in cement production from non-renewable energy sources such as coal and other fossil fuels. As a result, we release a lot of CO2 from producing cement.
In Laying the foundation for zero-carbon cement, McKinsey breaks down the sources of energy consumption and CO2 emissions throughout the cement manufacturing process.
The video below shows this process.
Despite improvements over the last 30 years, cement production remains highly inefficient from an emissions perspective. The chart below from the McKinsey article we referenced earlier is quite revealing.
KG of CO2 Emissions per $ of Revenue
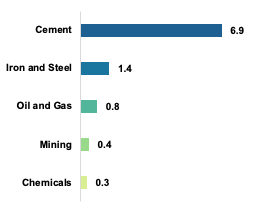
Net-Zero: What Must Be True
To hit net-zero by 2050, we need to eliminate the emissions from all stages in the concrete manufacturing process.
Eliminate emissions that come from powering the manufacturing process
Eliminate emissions that come from heating during the manufacturing process
Eliminate by-product emissions (CO2) that come from making cement
The first two will happen if we can fully transition from fossil fuels to clean energy sources.
The third happens if we can reduce (or replace) limestone in the manufacturing process.
Eliminating emissions from all three will be unlikely, so we will need to supplement our efforts with carbon capture, utilization and storage technology. These technologies involve implementing systems that capture emitted carbon and store it away from the atmosphere (for example, deep underground).
The biggest hurdle to eliminating emissions is an economic one. Industry incumbents need an incentive to change. Suppose green concrete is more costly than regular concrete. In that case, manufacturers will be at a competitive disadvantage if they adopt green cement, but their competitors don’t. To incentivize the production of clean concrete, we need to produce it for equal or less than the cost of regular concrete. Until we reach that capacity, we have a green premium—driving the green premium to zero means producing net-zero concrete at the same cost as concrete today. Currently, Breakthrough Energy estimates the green premium for cement is between 75-140%.
Concrete Green Premium
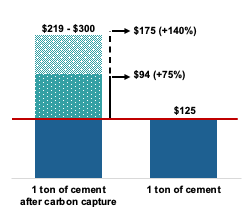
While we have progressed towards a net-zero transition over the last 30 years, we’re not even close to where we need to be. Check out the graphs below from the Global Cement and Concrete Association (GCCA). Keep in mind that we’re now less than 30 years away from 2050.
Concrete Emission Reductions Since 1990
Given the importance of concrete and its significant contribution to GHG emissions, a ~20% reduction in emissions over the past 30 years is simply not enough. We need to do more to achieve net neutrality by 2050.
As a first step, the GCCA has pledged to achieve net-zero emissions by 2050. The GCCA comprises the world’s 40 most prominent concrete producers, representing approximately 80% of the industry outside of China. China, however, represents over 50% of global cement production. Alongside the GCCA, several major Chinese cement and concrete companies, representing ~20% of the Chinese market, have also agreed to join this mission.
GCCA’s Commitment to Net Zero Emissions
Solutions
Reducing carbon emissions in the cement production process requires solutions that accomplish one of three things:
Replace fossil fuels with clean energy
Reduce or replace limestone in the production of cement
Capture, store, and re-use carbon
There are plenty of solutions, and it would be impossible to cover them all. The table below provides an overview of the important ones we found.
Category 1 - Replacing Fossil Fuels
Coal and petcoke, two of the most carbon-intensive fuels, are typically used to heat cement kilns. Replacing carbon-intensive energy sources in the cement production process can reduce CO2 emissions from cement production by up to 40%. One method of decarbonizing power in cement production is co-processing. Co-processing uses waste that can’t be recycled or reused as alternative fuels and raw materials (AFRs) in the cement manufacturing process. Alternative fuels (AFs) contain recoverable energy that replaces fossil fuels and alternative raw materials (ARs) act as substitutes for the raw mineral components in cement production. Typically, this waste would instead be incinerated or left at landfills. Here’s a good video that walks through this process.
AFs can be used as clean fuel by installing waste feed points to cement production facilities. AFs need to be fed directly into the high-temperature zones of the system (areas 2 and 3 in the image below) since they contain components that would otherwise be volatilized at lower temperatures. ARs generally follow the same kiln feeding process as traditional raw materials (area 6 in the image below). Note that the image depicts the production process from right to left.
Co-processing helps decarbonize electricity and remove harmful waste from landfills. While up to 100% of fossil fuels can be substituted by AFs, restrictions such as including local waste characteristics or permitting conditions could prevent that from happening.
One of the large players in this field is Geocycle, a multinational waste management services company that operates 180 co-processing facilities. Geocycle manages more than 10 million tons of waste annually and serves over 50 countries worldwide. Geocycle is the waste management division of Holcim, a global cement and concrete manufacturer.
Category 2 - Reduce or Replace Limestone
Supplementary Cementitious Materials (SCM)
SCMs are materials that can be added to the cement mixture to improve the properties of the concrete, including reduced permeability and increased strength. SCMs can reduce the amount of limestone needed in the cement, thereby reducing the amount of CO2 emitted in the calcination process. Two common SCMs are fly ash and ground granulated blast furnace slag (GGBS), which are by-products of coal-generated power and steel production. Using SCMs not only reduces the carbon footprint in cement production, but also helps remove harmful by-products from the environment. For example, fly ash can cause environmental damage by contaminating drinking water.
The amount of CO2 avoided by using SCMs is significant. Below is a table showing the differences in CO2 emissions between limestone and the SCMs mentioned above.
Still, current developments will only serve as short-term solutions. Both coal-generated power and steel production emit GHG, and clean alternatives will be necessary long-term. As we move towards more sustainable and clean energy globally, coal will be phased out, and indirectly, fly ash as a by-product. Also, as steel production becomes more efficient and environmentally sustainable over time, GGBS as a by-product will diminish.
Even if there was an abundant supply of these by-products, their calcium content is low compared to limestone. That means they cannot fully replace limestone in cement production. Unless a sustainable alternative is discovered and universally adopted to replace limestone, SCMs will only serve as a short-term solution.
There is hope, though. We only touched upon two common SCMs, but there are plenty of alternatives.
Researchers continue to search for SCMs that are abundant, easily accessible, and clean. For example, researchers at the Martin Luther University Halle-Wittenberg in Germany and the Brazilian University of Pará discovered that Belterra clay could serve as an SCM and replace at least 50-60% of limestone in cement production.
Also, in a 2018 research paper co-authored by the UN Environment, two SCMs are highlighted as having high potential.
Two clinker substitution technologies, calcined clay plus limestone and engineered filler combined with dispersant, make much higher levels of clinker substitution possible than previously expected. The sources of raw materials are almost unlimited and available virtually everywhere. The limits of adoption are related to minimum clinker imposed by the technical performance in different applications and environments. These technologies require modest adaptations in the existing production lines, and are expected to have small or no effect on costs. They can be deployed rapidly because they require only modest capital investments on plants and allow the clinker fraction to be reduced progressively as R&D advances and the industry gains experience.
Companies developing solutions in SCMs include Ecocem, backed by Breakthrough Energy Ventures, and CarbiCrete, backed by SQN Venture Partners.
Recycled Concrete
Concrete is 100% recyclable. However, not 100% of concrete is recycled. Most recycled concrete goes to lower-value products, but researchers and engineers are searching for ways to use recycled concrete for new buildings. Recycling concrete in the same site can save raw material and transportation costs. In addition, recycling concrete can lead to increased carbon capture through cement recarbonation. The European Circular Economy Stakeholder Platform explains this well:
Cement recarbonation refers to the process where part of the CO2 emitted during the cement production is re-absorbed by concrete in use through carbonation. Carbonation is a slow process that occurs in concrete where lime (calcium hydroxide) in the cement reacts with carbon dioxide from the air and forms calcium carbonate. At the end of their useful life, buildings and infrastructure (reinforced concrete structures) are demolished. If the concrete is then crushed, its exposed surface area increases and this increases the recarbonation rate. The amount of recarbonation is even greater if stockpiles of crushed concrete are left exposed to the air prior to reuse. In order to benefit from the CO2 trapping potential, crushed concrete should be exposed to atmospheric CO2 for a period of several months before its reuse (e.g. as road underlay). This needs to be taken into account in the way construction waste is dealt with.
HeidelbergCement, a German multinational building materials company, is focused on reducing its carbon footprint in the cement manufacturing process, and recycling cement is one of its strategies. They explain it well in this video.
Using Less Concrete
This one is pretty straightforward. We cut concrete emissions by using less of it.
A team of experts from the Universities of Bath, Cambridge, and Dundee recently demonstrated their ability to create a thin-shell floor that uses 60% less carbon during its construction than a comparable ordinary concrete slab, without sacrificing the amount of weight it can carry.
Here’s the explanation from the press release:
Currently most building floors use thick flat slabs of solid concrete, which are inefficient since they rely on the bending strength of concrete to support loads. Concrete isn’t very good at resisting the tension induced by bending, so these floors also need lots of steel reinforcement. Instead, ACORN’s approach is to use concrete for what it is good at - resisting compression.
By putting the material only where it is needed, and making sure it works in compression, the ACORN design uses far less concrete. The new shape might prove impractical to make using traditional temporary formwork, so the ACORN team has in parallel developed an automated adaptable mould and a robotic concrete spraying system that can be used in an off-site factory setting.
Since the floor is made off-site, it also needs to be transported to site and then assembled. This brought some exciting challenges for the team, who had to split the large floor into nine transportable pieces and develop a connection system to join the pieces together. However, this also brings some advantages, in terms of reducing time needed on-site for construction.
The ACORN team was also able to incorporate reversible joints, so that the floor can be disassembled and reused elsewhere at the end of the building’s life, promoting a circular economy for the construction industry.
Category 3 - Carbon Capture, Utilization & Storage (CCUS)
CCUS will be used across many, if not all, industries to reduce CO2 emissions. Achieving net-zero will be impossible without it as we cannot possibly avoid all anthropogenic carbon emissions. CCUS technology is broad-ranging and deserves a full write-up of its own, so we will keep it brief here.
There are many companies applying CCUS technology to the concrete industry.
CarbonBuilt is a start-up that has developed a carbon capture technology to take CO2 emissions from a coal production plant and cure the CO2 into its precast concrete. The company is backed by The Grantham Foundation and Climate Capital.
Heimdal is a start-up extracting CO2 from seawater to make carbon-neutral cement. The company was part of Y Combinator’s Summer 2021 cohort and has received subsequent funding from Liquid2 Ventures and Apollo Projects among others.
Holcim launched a full-cycle carbon solution project in Canada called Project CO2MENT. CO2 from the manufacturing plant is captured and will be injected into low-carbon fuels, carbon-cured concrete, and fly ash.
One emerging CCUS technology particular to cement manufacturing is calcium looping. Calcium looping uses calcium oxide as a sorbent to absorb CO2 emitted in cement manufacturing. The combined molecules are contained and subsequently separated, whereby the CO2 is stored and the calcium oxide is reused to repeat the process.
Carbon-cured concrete
With broader CCUS adoption, there is a growing market for the utilization of captured carbon. In the concrete industry, one development is carbon-cured concrete. Carbon can be injected into concrete to make it more durable, less permeable to water, and more resistant to cracking, freezing, and thawing. Typically, concrete needs to retain the right amount of moisture and be kept at the right temperature over some time (usually 28 days) to attain full strength. With carbon-cured concrete, full strength can be achieved in 3 days.
Carbon-cured Concrete - Process and Strength
Some start-ups innovating in this space include the previously mentioned CarbonBuilt, and Solidia, which is backed by Imperative Science Ventures and Zero Carbon Partners. However, the scope of these companies’ carbon-curing concrete is limited – currently, they can only manufacture precast concrete. A larger share of the concrete market lies within ready-mix concrete. The description and market size of both types of concrete is shown below.
Nevertheless, ready-mix solutions are being produced by other start-ups. One example is CarbonCure, a Canadian company backed by Amazon and Breakthrough Energy Ventures. Their carbon curing technology can be integrated into existing production facilities in one day without any business disruption.
Blue Planet Systems, a start-up backed by Chevron Corporation and Mitsubishi Corporation, manufactures carbon-cured aggregate, the filler mixed with cement and water to form concrete. The aggregate can be used to create both ready-mix and precast concrete.
Barriers to Adoption
We’ve covered many promising solutions to bring concrete emissions to net-zero, and our coverage is not exhaustive! However, that does not mean the road ahead is an easy one. While we are making technological progress, several barriers exist that will impede the adoption of these solutions.
Regulations
Barrier: Certain building codes include specifications on the chemical composition of concrete. These specifications could rule out green concrete from being used even if it meets all the performance specifications.
Development & Mitigation: Adoption of preferential treatment of green concrete. For example, in 2019, New York Assemblyman Robert Carroll introduced a bill in the New York State Assembly that would give preference to lower carbon concrete in the bidding process for state-funded projects. New Jersey has a similar bill.
Reliability / Safety
Barrier: There is a significant risk involved with the early adoption of a technology that is meant to support bridges, buildings, and homes. Structural reliability will need to be wholly assured for the technology to be adopted. Even then, it is always easier for people to default to the status quo without economic incentives or policy intervention.
Development & Mitigation: Regulatory testing provides reassurance to and removes liabilities from construction companies. For example, regulatory testing proves Carbicrete is 30% stronger than conventional concrete.
Short-Term vs. Long-Term Thinking
Barrier: Many organizations have a short-term and a long-term plan. The allure of achieving short-term goals (e.g., reducing emissions by 30%) at the expense of achieving long-term goals could result in inefficient resource allocation for a net-zero future (e.g., prioritizing developments in sourcing and using fly ash and GGBS in cement over R&D for more effective and abundant SCMs)
Development & Mitigation: Large cement manufacturers are already demonstrating their ability to prioritize the long-term outcome. HeidelbergCement announced that they are building the world’s first carbon-neutral cement plant, expected to be fully scaled by 2030.
Intellectual Property
Barrier: Patents protect the economic benefits of innovation for their creators. Unfortunately, patents and expensive commercial licenses often slow the overall productivity of nascent and innovative industries. Competition often gets in the way of innovation as the same protection offered to the creator prevents others from utilizing the technology to enhance their production scale or improve upon the technology.
Developments & Mitigation: Collaborations can mutually benefit companies by improving the odds of developing new technologies and sharing the financial rewards. A small piece of a large pie is better than a large piece of nothing.
Where We’re Headed
We’re optimistic for a future with sustainable concrete. 8% of global CO2 emissions is a lot to eliminate, but countless entrepreneurs are itching to find solutions, and the impressive commitments by incumbents to develop and adopt clean technologies are encouraging. It’s very possible to see a world in thirty years where most of the limestone in cement production is replaced by clean alternatives, the cement manufacturing heat is powered by clean energy, and any remaining carbon emitted is captured and reused or stored away from the atmosphere. Until that day comes, we hope to share and inspire more people to learn and get involved in the space!