Hello everyone 👋 If you’re new to our page, welcome!Â
This post will dive deep into the second-largest emitter of greenhouse gases (GHG) from making things – steel. If you’re unfamiliar with how we’re classifying the sources of GHG emissions, check out our about us page.
How Much Greenhouse Gas is Emitted from the Things We Do?
Our previous post covered concrete, the largest emitter of GHGs from making things. Like concrete, steel is everywhere. It feels like steel is more common in our lives than concrete. Beyond infrastructure, we use steel to make our cars, forks and spoons, beds, and laundry machines. It’s no wonder that we produce 1.9 billion tonnes of steel every year, generating US$2.5 trillion in revenue and employing around 6 million people. Those stats make steel the third most abundant man-made material on Earth, after cement and timber.
Like many of the things we use, steel is mostly made in China. Despite the geographical concentration, the industry remains competitive. The largest producer, Baowu Group, only produces 6% of total annual steel.
2021 Steel Production by Country
2020 Steel Production by Company
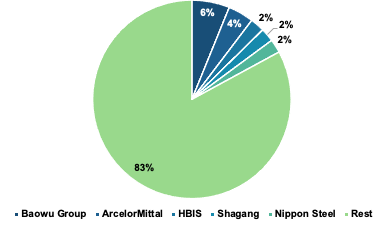
Steel demand can be grouped into four end markets: construction, machinery, vehicles, and consumer goods. The table below shows each end market's annual demand and current in-place steel.
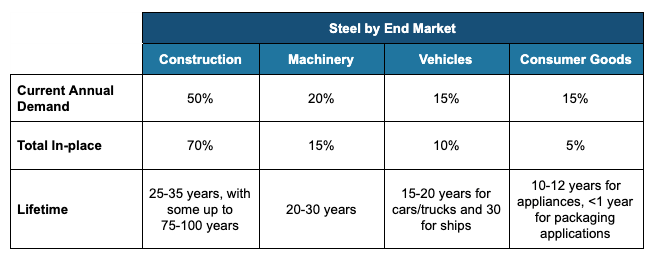
Steel is also critical for our clean energy transition. We use steel to build wind turbines, nuclear power plants, and solar roofs.Â
Since we can’t separate ourselves from steel, we’ll need to learn to live together sustainably. How? Let’s dive in.
Sources of Emissions
The steel industry directly accounts for about 2.6 billion tonnes of carbon dioxide (CO2) per year, roughly 7% of global CO2 emissions or 6% of global GHG emissions. The main culprit? Coal.Â
The steel sector is currently the largest industrial consumer of coal. Coal provides for ~75% of the energy demand in steel manufacturing. In 2019, the steel industry used 900 million tonnes of coal, about 15% of the global demand.Â
To understand why coal is used so much in making steel, we need to know how steel is made. It also helps to understand the difference between iron and steel - iron is a natural element found on Earth, whereas steel is manufactured by combining iron and carbon.
We generally produce steel using two types of furnaces:Â
Blast furnace-basic oxygen furnace (BF-BOF)
Electric arc furnace (EAF)
These two furnaces use different raw materials. BF-BOF uses iron ore, coal, and recycled steel, whereas EAF mainly uses recycled steel and electricity but can also use iron ore. EAF can support 100% of recycled steel as an input, but BF-BOF can only support up to 30% of recycled steel as an input. You can probably already tell which method is environmentally worse.Â
The specific steps in making steel using the BF-BOF and the EAF are similar when iron ores are used. We’ll explain the BF-BOF method and discuss the key differences to the EAF method.
There are three steps to steel production for the BF-BOF method:Â
Raw material preparation
Ironmaking
Steelmaking
1. Raw Material Preparation: Iron ores are heated and formed into small pellets, and coal is heated to make coke (not the soda). Coke is a grade of hard coal with a higher carbon concentration. It’s used for fuel and the chemical reaction needed for making steel. This chemical reaction is called oxidation-reduction (redox), and its primary contribution is to remove oxygen from the iron.Â
2. Ironmaking: Once the iron ore and coke are prepared, they are fed into the blast furnace (BF) at 1400-1500°C. The blast furnace's heat energy usually comes from coal or natural gas. Limestone and other additives are added to control for impurities and temperature. The result is hot molten iron.
3. Steelmaking: The hot molten iron is fed to the basic oxygen furnace (BOF) to make steel. In the BOF, oxygen is injected to lower the carbon content in the iron from ~4-5% to the required level for steel (~0.25%). Steel is then cast and delivered as coils, plates, sections, or bars.Â
When iron ore is used in the EAF, the method is called direct reduced iron-electric arc furnace (DRI-EAF). The key difference between DRI-EAF and BF-BOF is the redox reaction agent. DRI-EAF uses natural gas, whereas BF-BOF uses coke. The table below summarizes the production steps for each method.Â
When only recycled steel is used in the EAF, the process is straightforward. Recycled steel is simply melted with electricity to make steel.
Those are all the details needed to understand the sources of emissions and the solutions we’ll discuss. If you want to learn more about steelmaking, here is a good resource.Â
So, where do most of the CO2 emissions come from? Step 2. The BF-BOF and DRI-EAF methods use coal and natural gas to heat and create the redox reaction in ironmaking. These fossil fuels emit significant amounts of CO2. In contrast, using recycled steel in the EAF skips steps 1 and 2, avoiding the associated emissions. As a result, steel made using 100% recycled steel in the EAF emits minimal CO2.

Unfortunately, the least environmentally friendly method (BF-BOF) is most common. Though the EAF method was invented in the late 19th century, it only grew in significance once the recycled steel supply increased (a recent phenomenon). In 2020, BF-BOF and EAF represented 73% and 26% of global steel production (other methods represented the remaining 1%).
2020 Production by Method (Top 6 Producing Countries & Global)
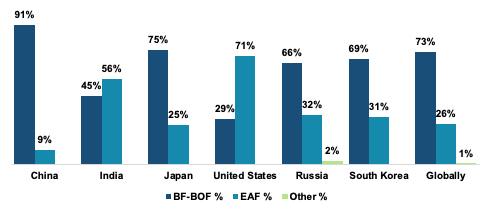
Steel contributes to a significant amount of CO2 emissions in various end markets. From buildings to cars to wind turbines, steel makes up between 30-50% of each products’ total emissions.
Supply-chain and Manufacturing Emissions by Product

Net Zero: What Must Be True
To reach net-zero emissions in steel production, we need to
Replace coal and natural gas as redox agents with carbon-neutral alternatives
Power the heat required in steel production with clean energy sourcesÂ
The current options aren’t great. Many of the solutions available today help reduce emissions but not eliminate them. The International Energy Association makes this clear in their net-zero 2050 forecast for the steel industry. In that forecast, nearly 75% of the annual emission reduction comes from current pre-commercial technologies. This makes our situation challenging – we must balance investing in solutions that guarantee reduced emissions now and investing in novel technologies that can eliminate emissions. We’ll discuss both types of solutions, but keep the long game in mind as you read. Short-term wins often run the risk of making us deviate from the actual target: net-zero emissions by 2050.
Breakthrough Energy estimates the green premium of carbon-neutral steel by using Carbon Capture, Utilization, and Storage (CCUS) technology is currently between 16-29%. This premium is much lower than the green premium of 75-140% for concrete discussed in our last post. However, using CCUS to sequester all CO2 emissions has practical limitations. Even without these limitations, we would still need to bring the green premium down to zero for green steel to be cost-competitive – especially in a commodity business like steel.Â
Green Premium for Steel
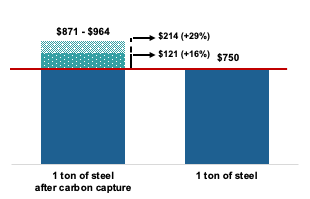
Despite a green premium, buying carbon-neutral steel might still be attractive for a company due to political and social pressure. Governments want companies to produce more green steel, and customers want things that are better for the environment. If companies can pass on the green premium to customers without dampening demand for their products, it’s an easy win-win situation. According to the World Economic Forum, if we used green steel to make a car, it would only increase the price of that car by 1% while reducing material-related CO2 emissions by up to 34%. Even customers who aren’t climate-conscious would look at that deal and think it’s a steel (pun-intended)!Â
With so much attention on sustainability, we’d bet that car manufacturers would be happy to promote eco-friendly cars even at a slight price premium. We’d also bet that many customers prefer eco-friendly cars when the price difference is immaterial. Increased sales of eco-friendly cars will increase green steel demand and production scale, accelerating the pace of eliminating the green premium.Â
It would be great if we could rely on the markets to guide themselves to a green future, but unfortunately, that is not the world in which we live. Pressure needs to be applied across the supply chain to ensure that net-zero emissions are achieved quickly. Everyone is feeling the heat (literally). Steel manufacturers, including the two largest, Baowu and ArcelorMittal, have committed to net-zero emissions by 2050. Other manufacturers have pledged even more aggressive goals. SSAB aims to commercially sell carbon-free steel in 2026 and have all its production be free from fossil fuel by 2040.Â
An important development needs to happen for these pledges to become a reality - steel production needs to move off of BF-BOF to EAF. The BF-BOF method produces over 70% of the global steel supply, and the blast furnace can’t operate without coke due to technical issues. As a result, the BF-BOF method will never be carbon-neutral without CCUS. It is critical that we start replacing retired BF-BOFs with new EAFs.Â
Approximately 50% of Europe’s steel assets are up for reinvestment over the next 10 years. The type of reinvestment into these assets will determine the success of our transition to a green steel industry.Â
Steel buyers are also under pressure to commit to a sustainable future. SteelZero, an initiative by The Climate Group and Responsible Steel, two international non-profit organizations, is gathering commitments to procure 100% net-zero steel by 2050. It currently has 18 members, including multinational construction companies.Â
With that backdrop, let’s jump into solutions for reducing and eliminating emissions.
Solutions
Reducing or removing carbon emissions from steel production requires solutions that accomplish at least one of three things:
Reduce steel demand
Reduce or remove fossil fuels in the redox reaction in ironmaking
Capture, store, and re-use carbon
Since we use fossil fuels for their energy and the redox reaction in ironmaking, solutions under category 2 need to provide both a clean energy source and a redox reaction agent.
The table below highlights the solutions we will discuss.
Recycling
Recycling rates for steel are incredibly high. Steel is the most recycled material on the planet. Globally, around 85% of end-of-life steel is recycled. Even better, steel properties never change regardless of how many times it’s recycled. Every tonne of recycled steel saves 1.1 tonnes of iron ore, 0.6 tonnes of coal, and 0.05 tonnes of limestone.
Out of the 1.9 billion tonnes of steel produced each year, around 0.7 billion tonnes are produced using recycled steel. That’s over 36% of global steel demand fulfilled by recycling. The supply of recycled steel is expected to increase significantly in the coming decades as more infrastructure projects retire. At the same time, steel demand will continue to outpace the recycled supply for as long as economies continue to grow. The implication is that recycled steel cannot be the sole solution for achieving net-zero emissions.Â
Still, we should try to improve the recycling rate. Better sorting and separation techniques are needed to do so. An important part of recycling steel is separating it from contaminating materials. For example, copper is often wrapped tightly around steel in car parts that require magnets for separation and sorting. Steel is also used to reinforce concrete in construction and can only be recycled after crushing the reinforced concrete with heavy equipment. These issues can lead to high costs for separation and, therefore, recycling. Sometimes, the costs are so high that recycling doesn’t make economic sense. If we improve the separation and sorting techniques, we can reduce the cost of recycling and improve the recycling rate.
Reduce Steel Scrap
There are two steps between when steel is made at the manufacturing plant to when it is put into the final product:
Freshly made steel (crude steel) is rolled and processed into general shapes for delivery, such as bars, sheets, or coils (finished steel).Â
Finished steel is delivered to the customer, and the customer processes the steel again to meet their specific needs (steel in final product).Â
Some steel is scrapped in step 1 (home scrap), and some in step 2 (prompt scrap). Home scrap is generated at the steel manufacturing plant and is recycled immediately. Prompt scrap is generally high quality, uncontaminated, and recycled within a year. These scraps differ from end-of-life scrap, the leftover steel at the end of a product’s lifetime.
Remaining Steel After Scrap

By the time the steel goes into the final product, ~22% of the original crude steel has turned to scrap. While close to 100% of this scrap is recycled, it’s better if we produce less scrap because even recycled scrap needs electricity for processing.Â
Every year, home and prompt scrap represent approximately half of total scrap, with the remaining half being end-of-life scrap. By reducing home and prompt scrap, we can remove up to 50% of the emissions generated by processing recycled steel. Eliminating scrap is not the goal since scrap can be recycled and remade into steel without emissions after we solve for clean energy. However, while we’re still using fossil fuels to generate electricity, we should try to reduce scrap where feasible. For example, cutting body panels for vehicles from metal sheets generates a lot of scrap – up to 30%. Adopting more advanced manufacturing techniques like 3D printing can minimize scrap production. More efficient manufacturing isn’t just better for the environment; it also helps the manufacturer get more yield on the steel they buy.Â
Use Less Steel
Steelmaking has gotten more efficient. Over the past 30 years, we’ve reduced the energy required to make steel by 50%. Steel is also now stronger and lighter than before. We can rebuild the Eiffel Tower using only 33% of the original steel, and cars are now stronger but 35% lighter than before. And we can still further optimize steel usage with improved design and construction practices.Â
Another huge contributor to reducing steel demand is extending the lifetimes of buildings. Buildings are often demolished before the end of their useful life. Think about your neighborhood. I’m sure you’ve seen older buildings that could last for a few more decades knocked down to make way for new buildings. Developments are necessary, and we shouldn’t hold back economic growth. But, if these old buildings could be refurbished or repurposed as part of the development, we would need less new steel.
Biomass
Biomass is renewable organic material from plants and animals that can be used as an energy source. Certain kinds of biomass can replace coke in the redox reaction in making steel.Â
Biomass solutions are being developed but are not common in steelmaking. Rio Tinto is currently testing biomass with microwave technology to bypass the need for coke in steelmaking. ArcelorMittal is replacing a portion of coal with bio-coal at its Belgium plant.Â
Undoubtedly, biofuel is better than coal since coal is not a renewable energy source (it takes millions of years to form naturally). But, the sustainability of biomass as a solution depends on how it’s used. Plants capture and store CO2. When we burn plants for biofuel, the CO2 captured by plants is released into the atmosphere. The equivalent plants burned for biofuel need to be replanted to re-capture the emitted CO2. If that’s done, then biofuel presents a carbon-neutral solution. However, the effort and cost of re-planting is high, making adopting biofuel challenging.Â
Hydrogen-Based Direct Reduced Iron
The DRI-EAF process uses natural gas to drive the redox reaction in steelmaking. If we could replace the redox agent with 100% hydrogen and generate the hydrogen required using clean electricity, we could make new steel with zero emissions. There are currently a few projects developing this technology.Â
In Sweden, the Hydrogen Breakthrough Ironmaking Technology (HYBRIT) project piloted a plant in August 2020 using 100% electrolytic hydrogen from non-fossil fuel sources. In August 2021, a trial delivery of the first fossil-free steel was sent to Volvo Group. HYBRIT has a goal of bringing this technology to an industrial scale by 2026.
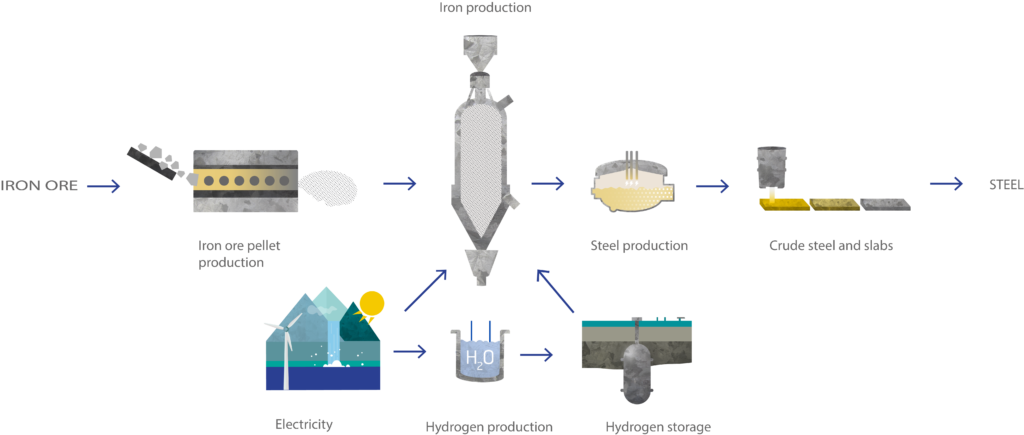
Similar projects by other steel manufacturers include ArcelorMittal’s pilot plant in Germany, the Salzgitter Low CO2 steelmaking (SALCOS) project by the Salzgitter Group, and HBIS’ demonstration plant in China.Â
Start-ups in the scene include H2 Green Steel, a Swedish company founded in 2020 that’s building a green steel production plant. It aims to be in production by 2024 and produce 5 million tonnes of green steel annually by 2030. The company is backed by Mercedes-Benz and Spotify co-founder Daniel Ek. Mercedes-Benz and BMW have pledged to use H2’s green steel in their cars starting in 2025.
Hydrogen-based DRI is promising, but there’s a major challenge. Although hydrogen is one of the most abundant elements in the world, it’s almost always found as part of another compound such as water or methane. The process required for extracting hydrogen in its pure form requires a lot of energy. Most of the world’s hydrogen is extracted in a CO2-intensive process called steam methane reforming (SMR), which produces hydrogen and CO2. A carbon-neutral method is water electrolysis, which uses an electric current to split water into hydrogen and oxygen. This technique is very electricity-intensive and thus is only carbon-neutral if the electricity is generated with clean energy.Â
Currently, the price of hydrogen generated without CO2 emissions (green hydrogen) is 2x more expensive than the hydrogen generated with CO2 emissions (grey hydrogen). However, green hydrogen developments will scale over time, and prices will fall. In contrast, the price of grey hydrogen is expected to increase over time as governments set explicit costs to CO2 emissions. McKinsey expects the price of green hydrogen to be equal to the price of grey hydrogen by 2030. At that point, producing green steel with 100% hydrogen could be cheaper than with the DRI-EAF method. Companies developing green hydrogen solutions include Green Hydrogen Systems and Hydrogen Rise.
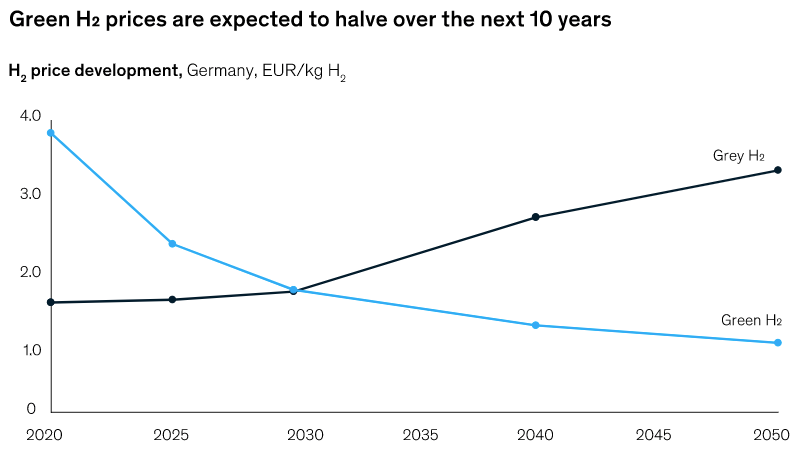
Direct Iron Ore Electrolysis
Direct iron ore electrolysis is similar to hydrogen-based DRI, except that it skips the step of producing hydrogen as the redox agent. Instead, it directly uses electrolysis to apply the redox reaction to the iron ore.
Boston Metal is a start-up developing a solution in this space and has raised money from Breakthrough Energy Ventures, BHP Ventures, Fidelity, and others.Â
Here’s a quick summary of the technology from Canary Media:
To start, the iron ore is melted with heat produced from electricity. Then it’s placed in a cell structured almost like a giant battery. At the top, an anode provides electric charge. At the bottom, a cathode receives the electric charge. In between, the charge flows through an electrolyte, which in this case is a scalding bath of molten materials. The electrolyte contains a variety of elements bound to oxygen, including aluminum, silicon and calcium.
All of these oxides are more stable than iron oxide, so the iron oxide is the first to separate when exposed to electric charge, breaking down into pure oxygen and iron. The iron, still liquified, sinks to the bottom where it can be tapped out and turned to steel.
This technology is still in its early stages. It has technical challenges, but if Boston Metal can produce steel using this technology at a commercial scale, it would be preferred over hydrogen-based DRI because it's more energy efficient. It’s estimated that Boston Metal’s technology can use between 30-60% less energy than hydrogen-based DRI. That’s considerable savings when you think about how much steel we make.Â
Hydrogen Plasma
A more advanced method of using hydrogen in steelmaking is also in development. SuSteel is an Austrian project using hydrogen plasma, which is much hotter than hydrogen gas, to make steel from iron ore in just one step. Hydrogen plasma heats and creates the redox reaction with the iron ores, while carbon is added to the iron to create steel. Because this method doesn’t require processing raw iron, it combines steps 1-3 of the DRI-EAF method. While promising, development is at a very early stage. It also requires a lot of clean energy to create hydrogen plasma, which demands a temperature of 20,000 °C.
Smelting Reduction
Smelting reduction is a more efficient method of steel production. The process is like the BF-BOF method but doesn’t require the preparation of iron ore and coke. Tata Steel is working on a smelting reduction project, the HIsarna project, that aims to improve energy efficiency and reduce CO2 emissions by 20% compared to the BF-BOF method. The process still emits CO2, but the CO2 emitted is more concentrated, so it’s easier to capture with CCUS technology. Combined with CCUS, the HIsarna project can reduce CO2 emissions by 80%. While promising, we need to make sure attention isn’t diverted from ways of eliminating CO2 emissions, even if the technology takes longer to develop.
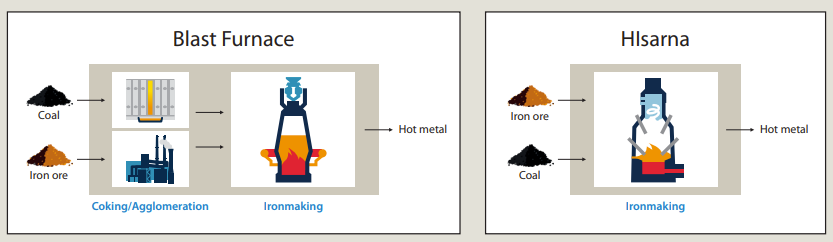
Carbon Capture Utilization and Storage (CCUS)
CCUS is promising but still in the early stages of adoption in the steel industry, both in terms of technology and market fit. There is currently only one commercial-scale CCUS installation in the steel industry, located at the DRI plant of Emirates Steel in the UAE. CCUS was installed at this plant in 2016. Since then, there hasn’t been a single other adoption of commercially-scaled CCUS technology in the steel industry. Why? Capturing and storing carbon is just an added cost to steel producers. If the explicit cost of carbon emission is lower than the cost of capturing and storing carbon, why would they bother? CCUS only made sense for Emirates Steel because they had a market to sell the captured carbon to – oil and gas companies. Oil and gas companies use carbon in enhanced oil recovery (EOR), a process whereby carbon is injected deep underground and mixed with the oil to increase oil extractability. Some of the carbon stored underground is released once mixed with the oil and extracted, but over 90% of it stays underground. Oil and gas companies are willing to pay for captured carbon and inject it underground because it makes them more money. There’s no other market that currently provides the same economic incentives, so CCUS technology doesn’t make economic sense for other steel manufacturers to adopt.Â
More use cases are being developed so that CCUS technology can be more widely adopted. ArcelorMittal is working with LanzaTech on the Steelanol project where CO2 from ArcelorMittal’s steel production will be captured and converted to ethanol. The first production of sustainable ethanol (bio-ethanol) from the plant is expected this year. Bio-ethanol can be used as a transportation fuel or for producing chemicals such as plastics. The EU-backed From Residual Steel gases to Methanol (FReSMe) project captured CO2 from steel production and used it to produce methanol fuel for ships. The demonstration project was completed in 2021, and recycled methanol fuel was used to power one of the largest ferries in the world. Now that it’s proven, hopefully the technology will be adopted by steel producers and ship transportation companies. Similar CCUS projects include Carbon2Chem in Germany and Carbon4PUR backed by the EU.Â
CCUS is promising and could drive a circular economy. For example, CO2 captured from steel production could be used for chemical production. The chemicals then could be reused in steel production through gasified waste in blast furnaces.Â
Implementation
Here’s what you should now know about steel:
Where the emissions come from
What needs to be true for the steel industry to hit net-zero
What solutions exist to drive down emissions
The final piece is an implementation plan for the net-zero transition.
1) START TODAY:Â
As we discussed, steel’s green premium is already pretty low compared to other industries.Â
Governments purchase a lot of steel for infrastructure and green projects like wind turbines. They can favor lower-emission steel by setting emission thresholds for their suppliers or offering a higher purchase price to clean steel providers. Large government contracts are attractive and represent a strong motivation for steelmakers to transition their business.Â
Consumers do not have the same purchasing power as governments and corporations but can still influence downstream products such as vehicles. Policymakers can support ethical shopping by instituting additional emissions transparency and limitations regulations.Â
2) ENFORCE LOW-EMISSION POLICIES:
Strict policies that favor green alternatives will accelerate the adoption of carbon-neutral steel. Even before novel steelmaking solutions are identified, we can begin breaking down the barriers they will face. For example, governments can apply policies that prevent high-emission facilities from being built. This will smooth the commercial adoption of green technologies as they are developed.
In the short term, policy and process innovations that support the circular economy will help reduce emissions. This includes promoting steel recycling and intelligent engineering (less steel and less scrap).Â
3) SUPPORT DISRUPTORS:Â
Steel production is costly. Start-ups need a lot of funding to compete with globally scaled steel manufacturers in a commoditized space. Not the best spot to be in. This obstacle might be contributing to the lack of start-ups in this space. Governments and private enterprises can support disruptors by increasing the supply of non-dilutive funding, developing manufacturing innovation ecosystems, and sponsoring projects.Â
We cannot rely solely on incumbents to solve the net-zero steelmaking conundrum. Innovators need a P&L-protected playground to experiment with large production processes.
Final thoughts…Â
It’s important to keep in mind the distinction between reducing emissions in the short term and investing in technologies that will get us to net-zero in 2050 (they don’t always align). We discussed several short-term and often policy-related solutions in the implementation section because truly net-zero solutions in steelmaking are still at an early stage. Technologies like hydrogen-based direct reduced iron, direct iron ore electrolysis, and hydrogen plasma have the chance to revolutionize the way steel is made. We must continue to provide financial, government, and media support for these solutions if they are to become the norm someday.Â
If you’re looking to get your hands dirty, greenifying the steel industry is still an unsolved problem!